Company Name | Contact Info | Location | ||||||||||||
---|---|---|---|---|---|---|---|---|---|---|---|---|---|---|
SARIGÖL KONVEYÖR SİST. MAK. YEDEK PARÇA NAK. İTH. İHR. SAN. VE TİC. LTD. ŞTİ.
PAZARSUYU KÖYÜ 2. OSB 5. CAD. NO: 11 / BULANCAK / GİRESUN / TÜRKİYE
|
Contact Info: +90 454 355 5555
|
Hall: 3
Stand: 306/A
|
||||||||||||
Product Groups | ||||||||||||||
No product group found |
- Company Info
- Products
- Represented Companies
- Company Brands
Our company plays an important role in the machinery industry today with its almost 20 years of experience. Our company is especially specialized in manufacture of chip conveyors and leader of market in this field. Sarigol Conveyor contributes to the country s economy with its exports to European Union countries as well as with domestic sales. In recent years, the other matter our company gave importance to are chip conversion systems. This system allows us to exclude chips from toxic waste extent and prevents them from harming the environment. In addition, coolant/oil become reusable when seperated from the chip and this system allows companies to save money. Quality products, customer satisfaction and importance to R&D activities are important features which make our company a leader in the sector. Another feature that makes Sarigol Conveyor a leader in the sector is timely and unlimited aftersale technical support. Our company has TSE and CE certificates and has been manufacturing in a more modern and large factory ever since recent investments were made. Our company always believes in the future of Turkey and agreed to continue investments as a company policy in this direction.
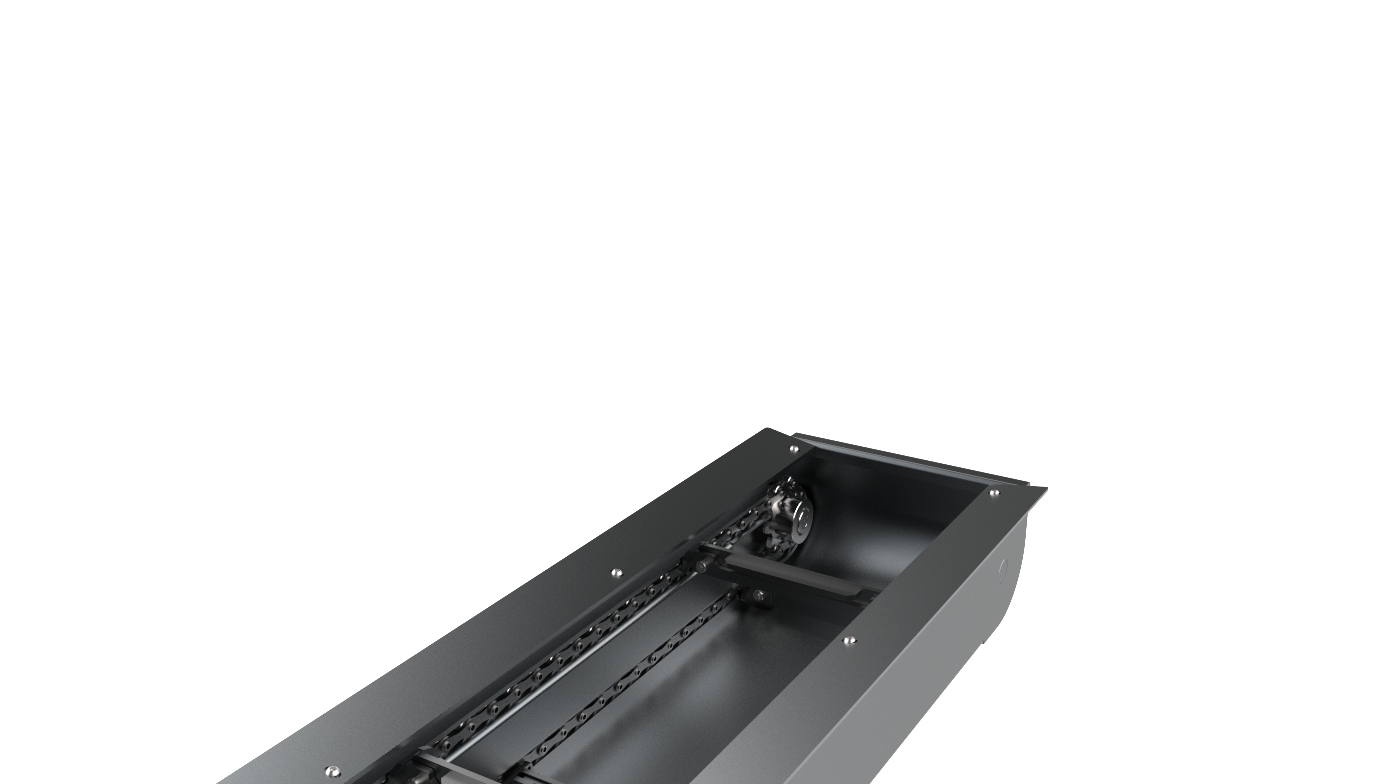
Hinged belt conveyosr are used to convey a broad range of long, rough, curled and crumb type chips which come from from transmission steel, work tool steel, aluminum alloy metal, as well as other materials such as teflon, delrin, etc. Hinged belt conveyors are most commonly used type of chip conveyors. Scraper conveyors are used to convey small chips and particles which come from grinding and honing various composite materials such as iron, cast-iron, brass-alloys, and sintered metals. Scrap Conveyor this type of conveyors are mainly used for discharge of metal parts from press machines. It is very similar to the belt system used in hinged belt conveyors. The biggest difference is that the parts that come out of the presses are very thin from time to time and scrap have a structure that prevents them from entering in between belt links. In this way, all kinds of large and small parts can be discharged without any problems. As in other conveyors, it can be produced in desired dimensions. Accessories such as pumps, switches, level controllers, brush system or oil skimmers on the conveyor can be added according to the customer s demand or need.
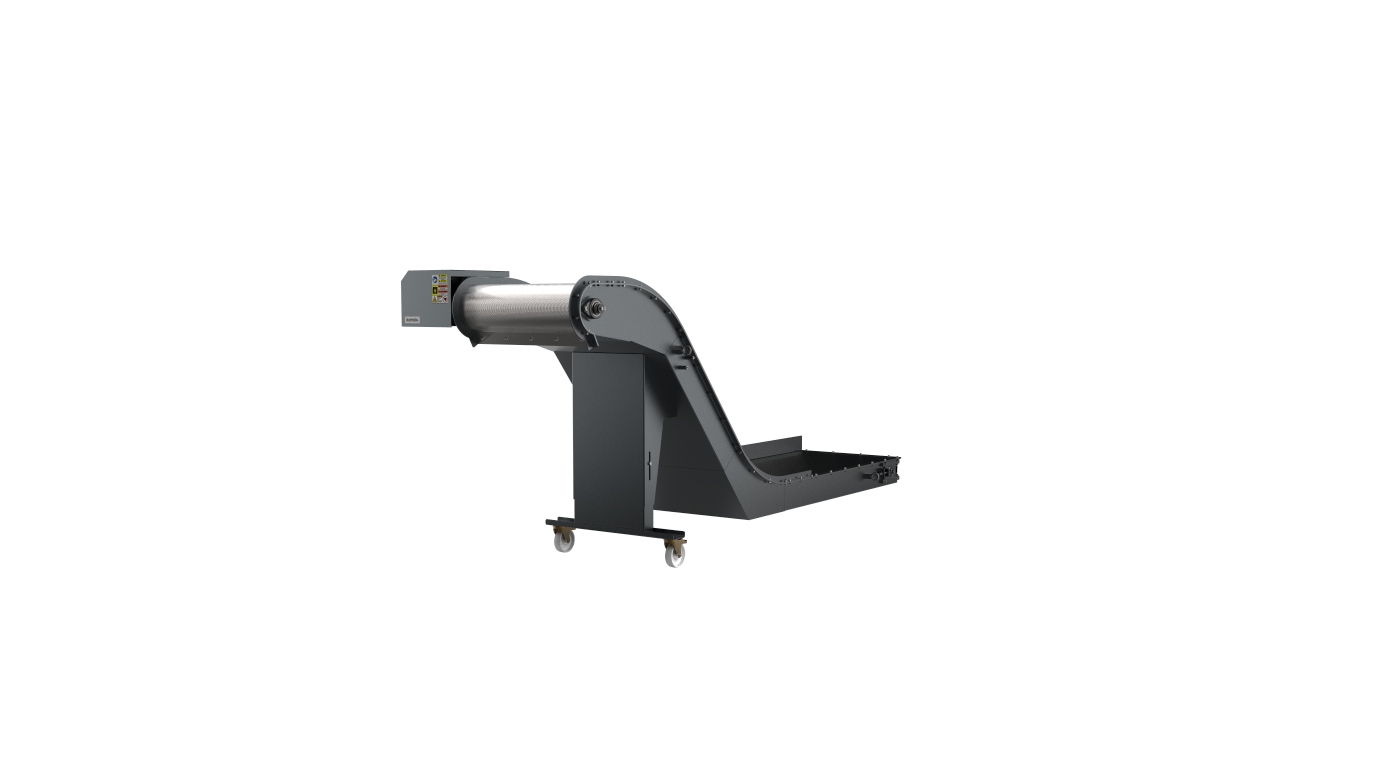
Magnetic conveyors are used to carry dust, crumbed iron chips, and other metal particles.
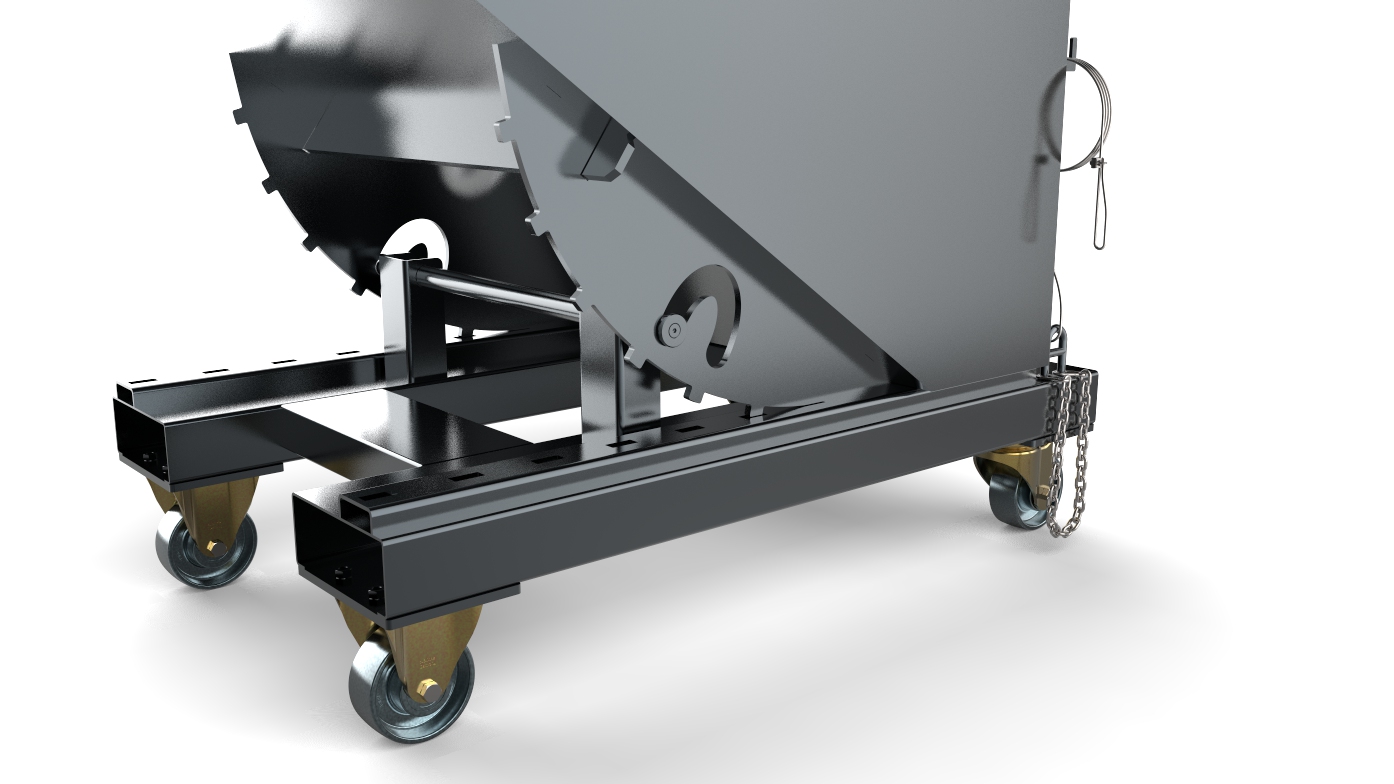
Chip carts are braked and tilting wheeled carts which are used for collecting chips which come from chip conveyors. It can be easily moved under conveyors and emptied to chip storage with its special design.
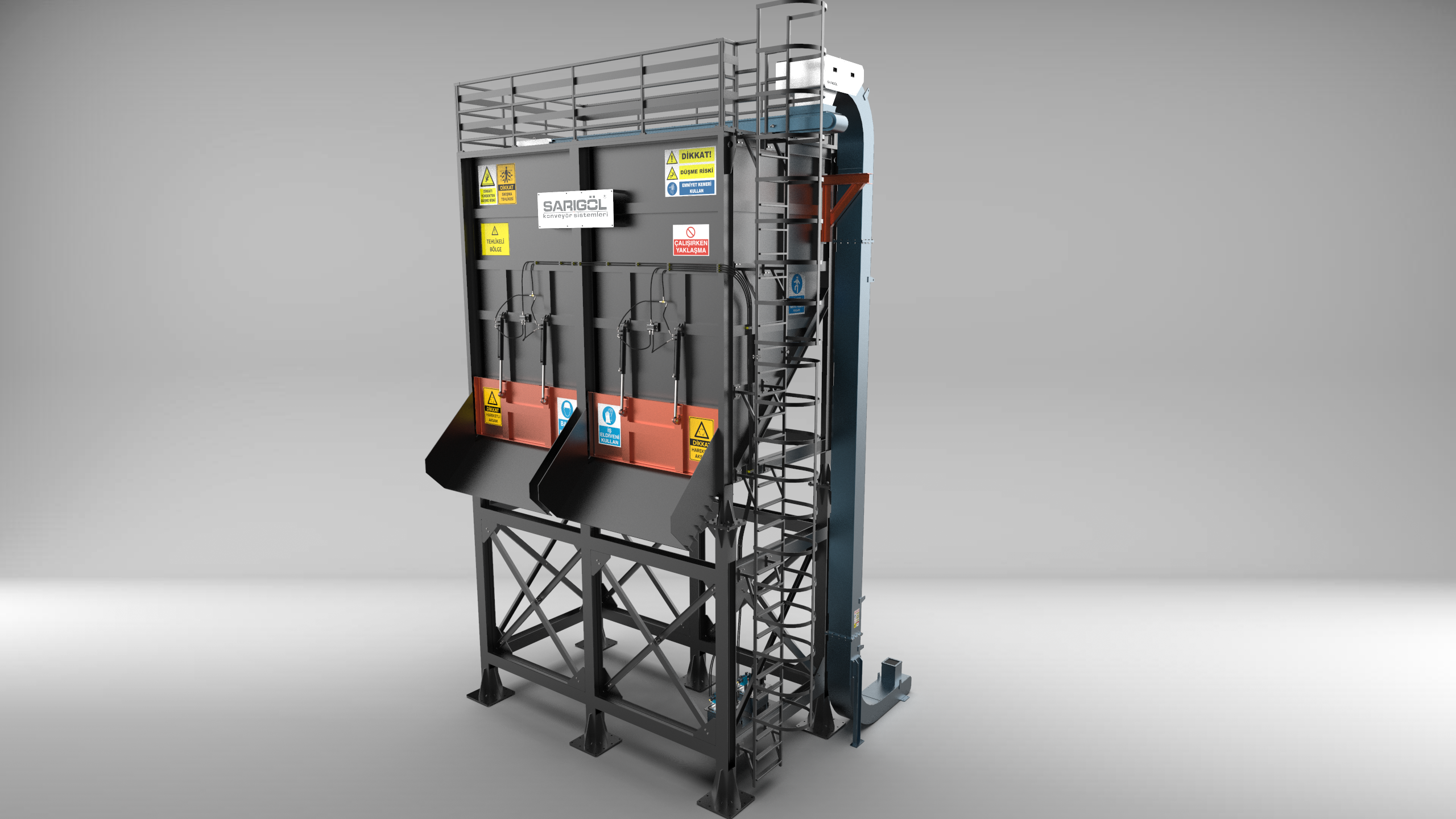
Chip silos are used to store high capacity chips which come from line conveyors and to transfer chips to trucks when required.
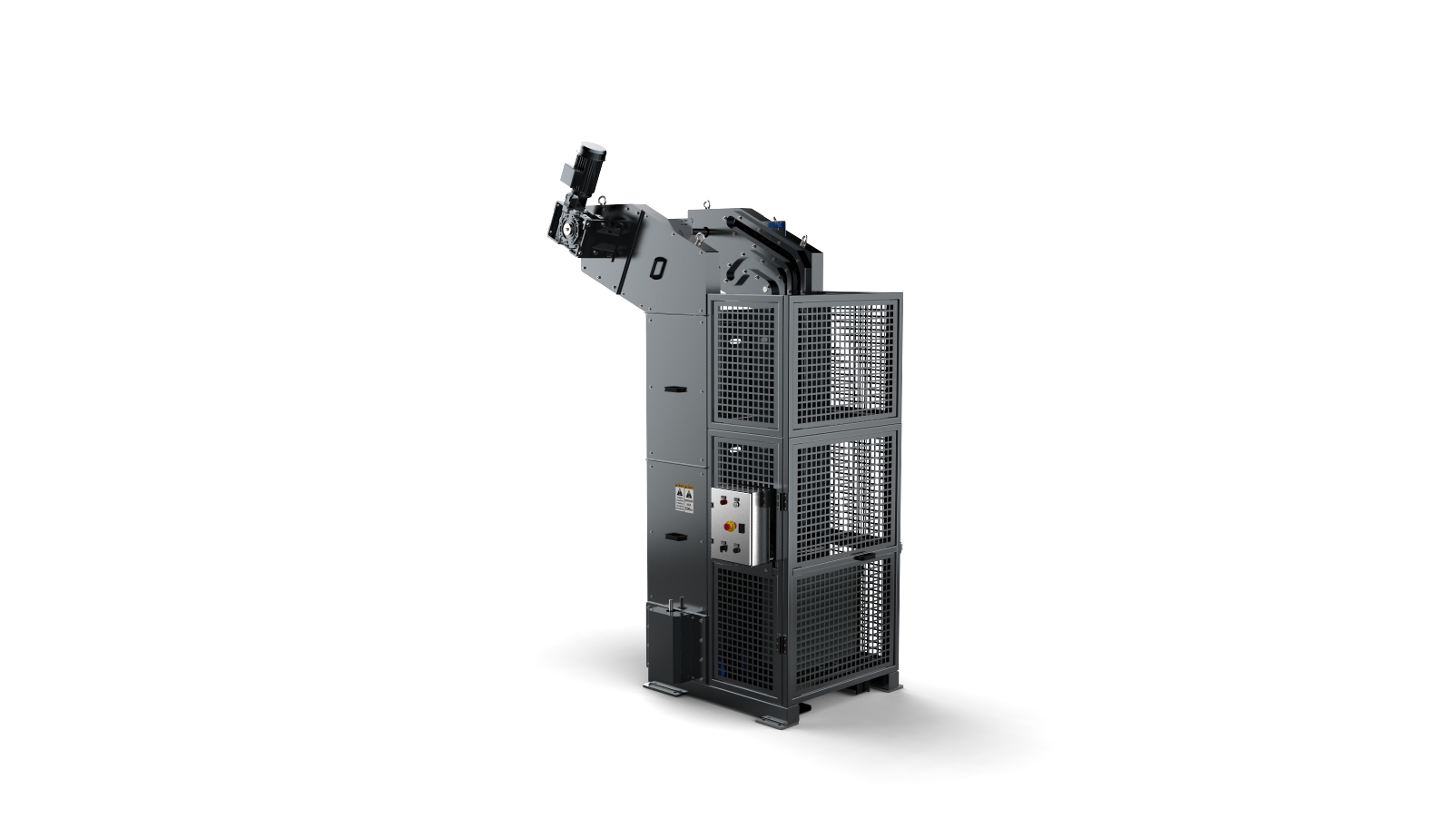
This device is used to load chips which come out from machine tools to available containers or silos by chip carts.
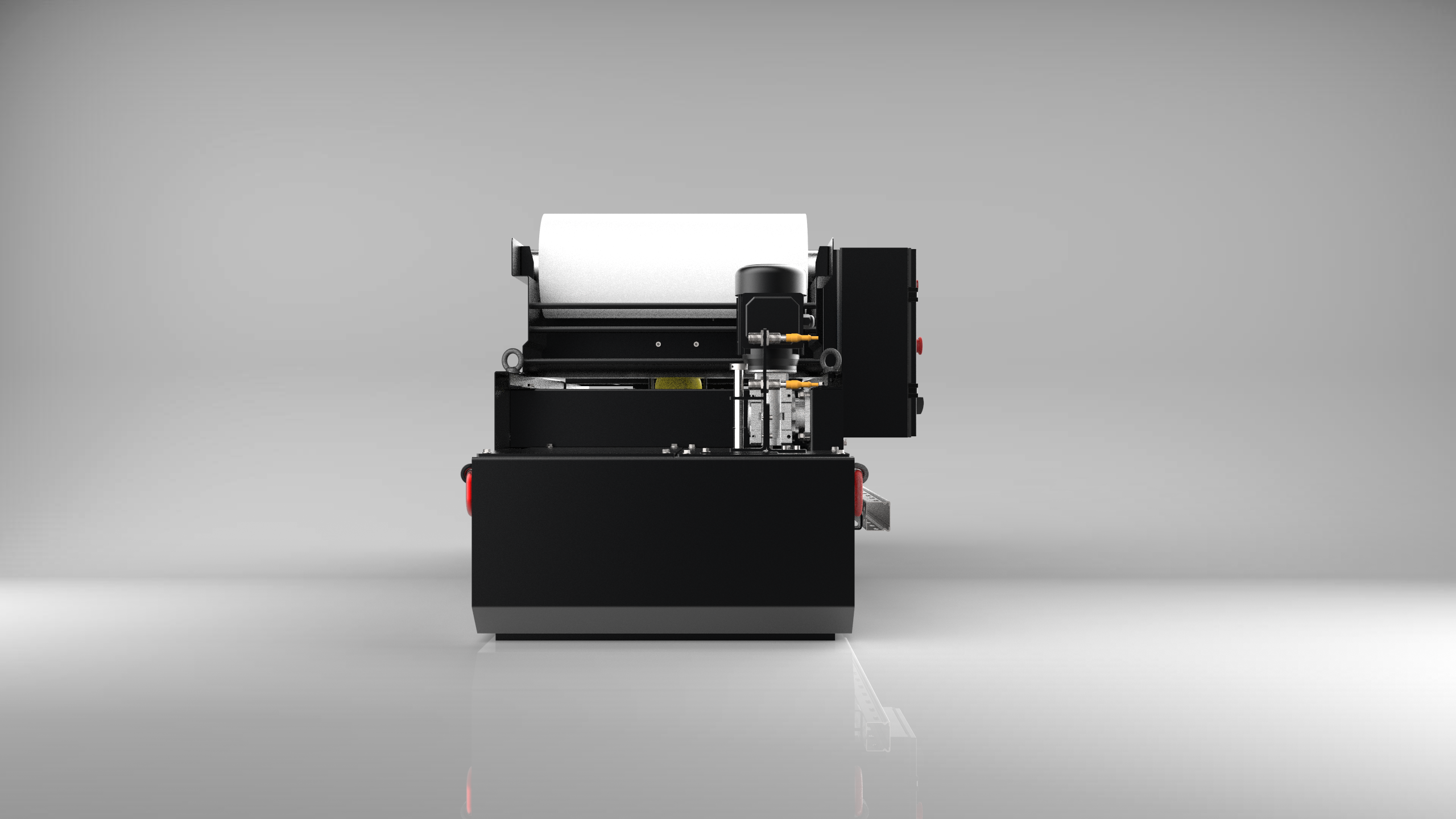
Seperator is designed to be uses for, machining centers, machine tools and grinding machines where clean coolant is needed; honing centers; and pumping stations which allow particles at micron level.
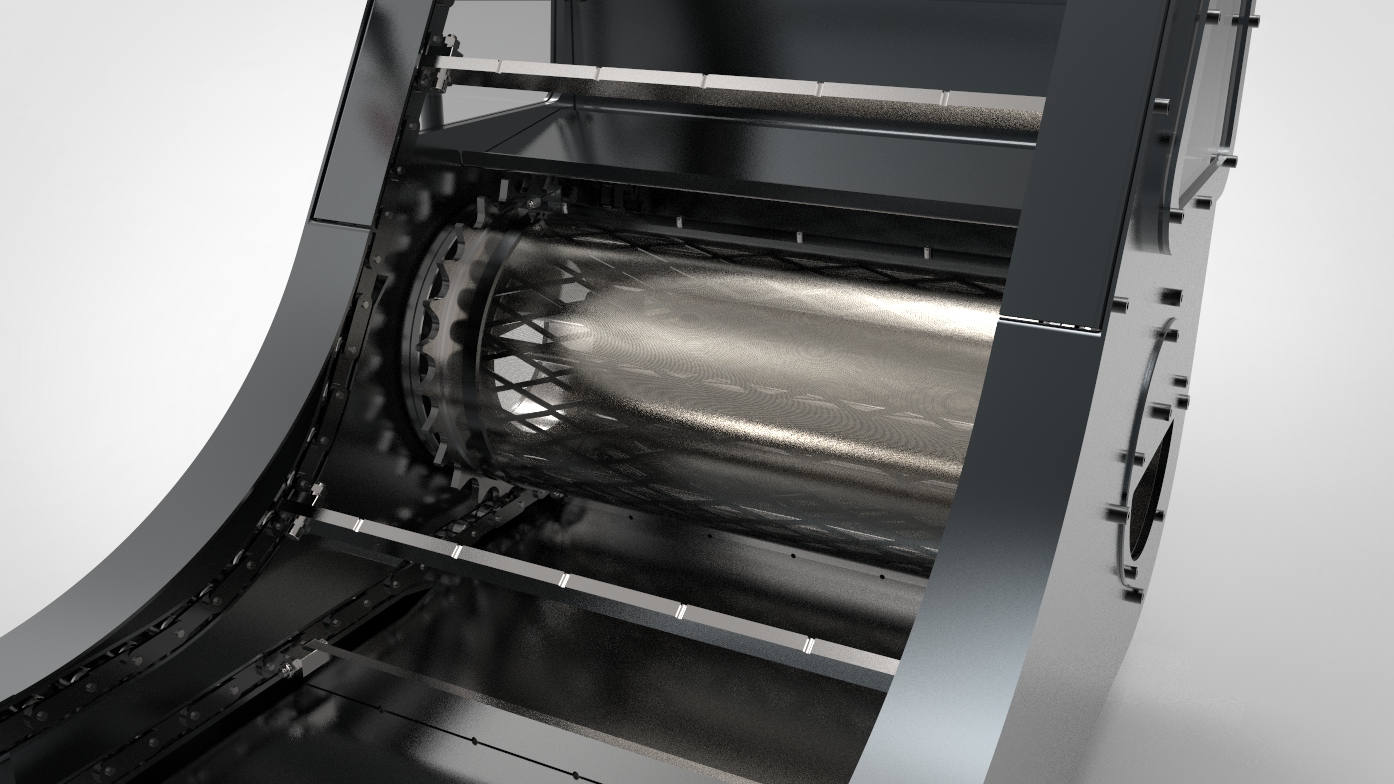
Drum filter unit ensures problem-free conveying dusty chips and crumb chips with its special designed drag conveyor system. Filtered drum filters coolant around 50 microns and makse it possible for reuse in the system.
Central filtration systems enable the filtration and recycling of multiple processing center refrigerant liquids in a single place at the production plants that manufacture machining.
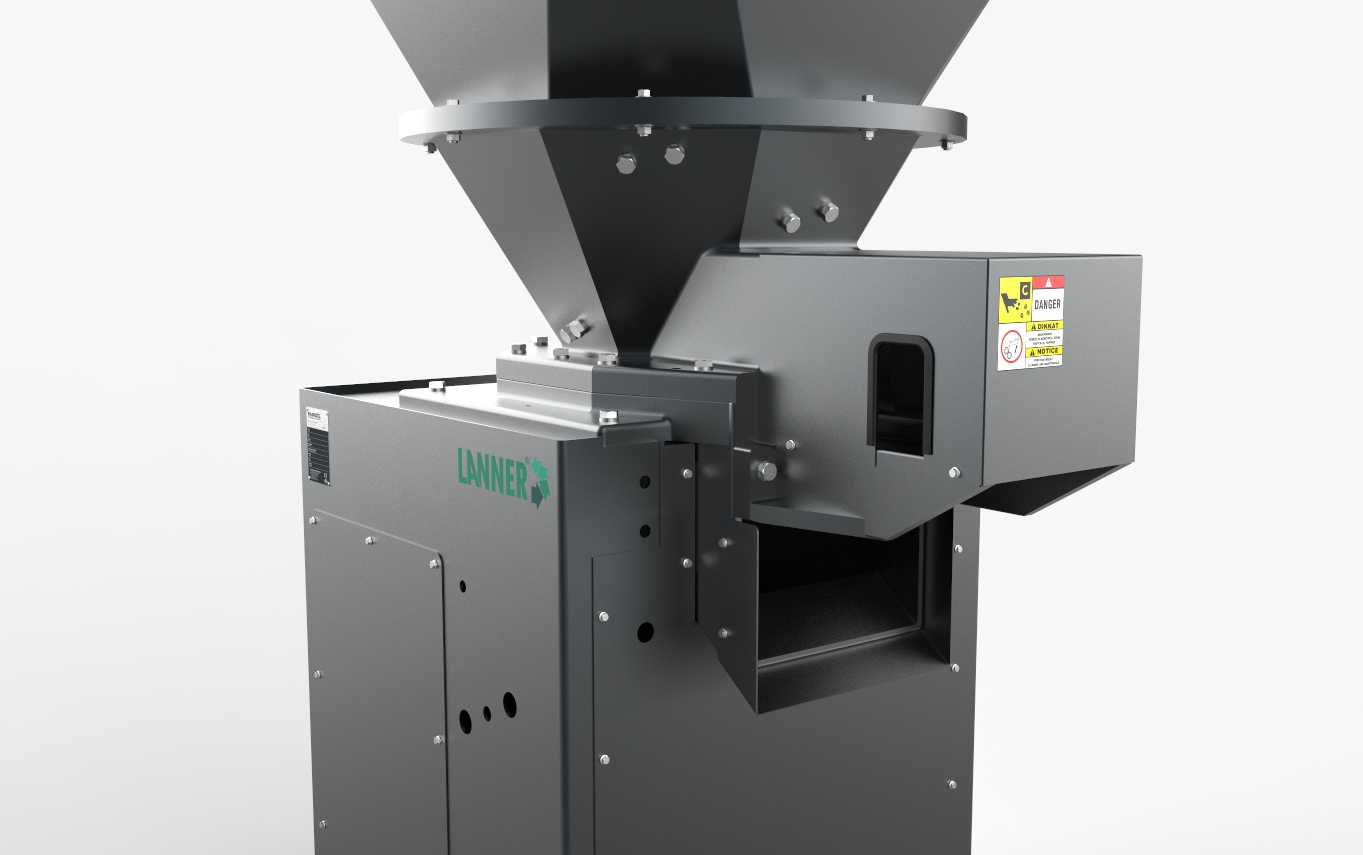
The woolly and long chips with coolant content, which have to be crushed are fed with a conveyor or chip cart dumper into the infeed hopper of the chip crusher. A rotating knife head with hardened crushing tools moves the complete chip ball against the hardened tearing blocks fixed on the crushing hopper. The precrushed chips fall downwards into the crushing mill, where they are crushed to a minimum size. Mistakenly initated tramp metals such as bar ends and tools canbe ejected. Even tough chips can be crushed with this chip crusher. The chip crusher can be extended e.g. with an automatic diverter chute, with special material for life extension or with an electro-magnetic locked inspection cover on the infeed hopper.
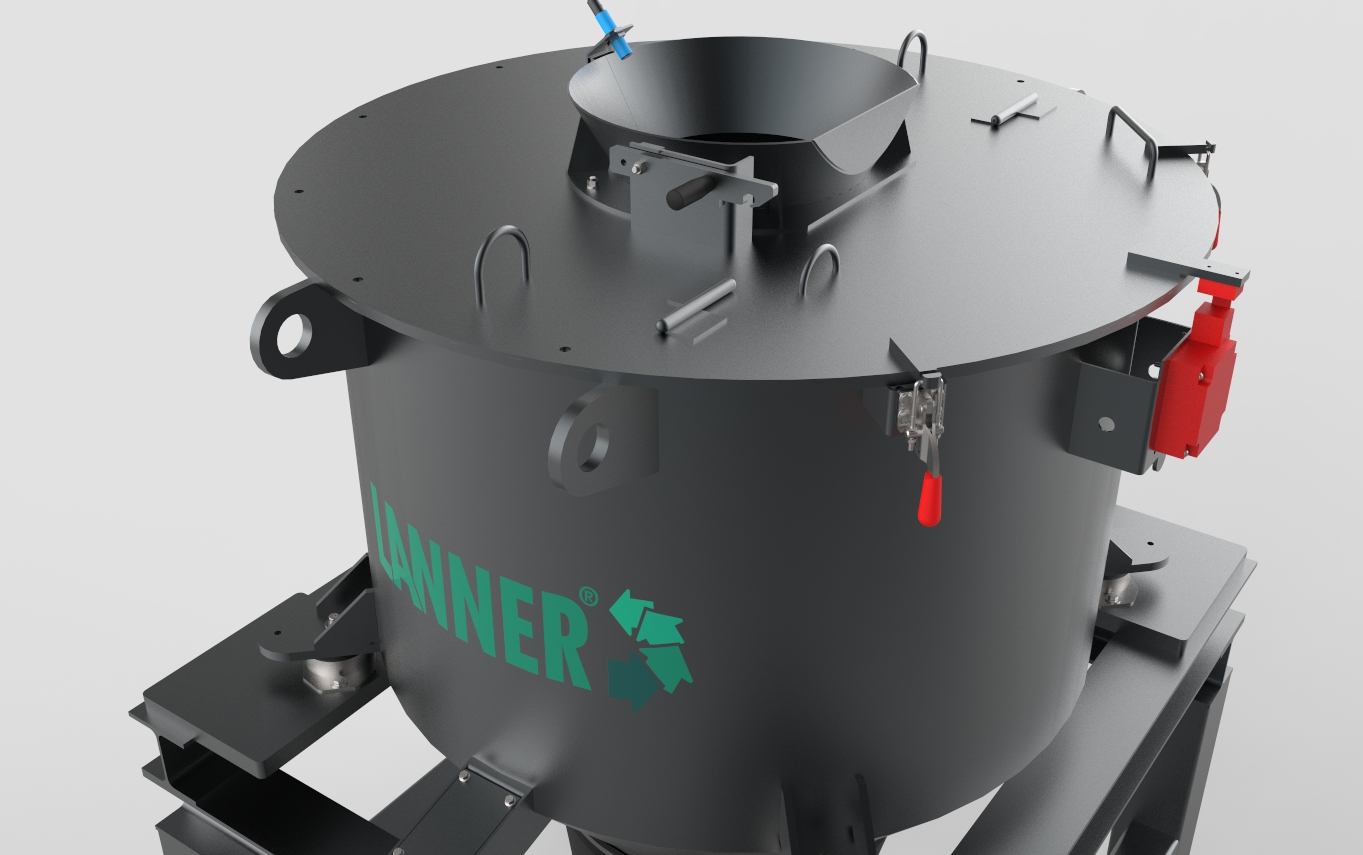
Lifting Bottom Centrifuge, Coolant containing chips or sludge falls over the infeed hopper into the rotating drum of the lifting bottom centrifuge. At this point the material is touching the lifting bottom and is moved against the drum wall under high centrifugal forces. At this point it is forming up in a ring and is moved in cycles up onto the slot sieve where the liquid is separated. Each cycle of pushing is moving the material Upwards over the slots of the sieve until it reaches dried the edge of the drum, flied against the inner housing wall and drops down through the outlet hopper. The hydraulically activated lifting bottom moves the chips and/or the sludge upwards to the slot sieve where the liquids are separated from the chips. After a few lifting cycles the centrifuged chips are carried over the edge of the drum and quit the centrifuge into the chip cart or discharge conveyor. The centrifuged coolant can be returned to the production or pumped back to further treatment. Parabolic Centrifuge, Coolant containing chips are falling over the infeed hopper into the rotating drum of the Paramax parabolic centrifuge. The centrifugal force presses the chips against the drum wall and they move upwards onto the slot sieve. At this point the coolant is separated from the chips The next infeed chips are pushing them over the edge of the drum and these are leaving the centrifuge downwards into a chip cart or discharge conveyor. Batch Wringer Centrifuge, The basket can be elevated into the centrifuge using a lifting hook. When the drum is placed into the centrifuge an individually set centrifuging time begins to run. After completion of the centrifuging process, the drum is taken out and the process can be repeated with the next wet material. Batch wringer are constructed for a long lasting continuous operation. The electro-magnetic lid locking, an unbalance detection switch and the standstill control provide maximum operational safety.
No represented companies found.
The company has no registered brand information.